The good news was the Fed Ex man was able to get it here without too much drama. The box was in good shape, and I watched him carry it up the drive. About 50 lbs.
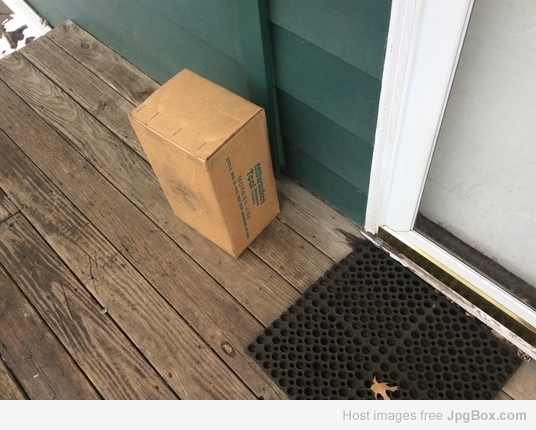
Ill start right at the beginning. Morgan calls this a machinists vise. I do not. It is not a Wilton, and is a bit sloppy in and out compared to a Wilton. I wanted a utility vise to mount on the bench, higher than the Wilton on the post, that had the ability to swivel. It will work perfectly for that. There is no anvil on the Morgan vise, a good thing, I think.
The vise jaws might be the nicest Ive ever used, very uniformly cut with flat diamonds, with T shaped backsides that are pinned from the back of the jaw. This eliminates the holes for the screws getting mashed when you clamp something. Only these jaws are available for this model vise, there is no smooth jaw option. The jaws are 1018, hardened to around 54c. I have half a notion to order another set of jaws, and put them on the surface grinder, to make my own set of smooth jaws.
One thing that bugged me was the lousy paint applied at the factory. Not as in paint you want to wax, but, I just wanted good quality, with even coverage on all parts to keep the rust at bay. I think the vise was assembled with lube, and the thing was hit with a mop of paint. Lots of uncovered and thin areas, and grease that had a coat of paint on it. Terrible quality. The color was safety blue. I had the chemistry on hand to mix continental blue, I think the number for safety blue is 7724, continental blue is 7729, very close match. I cleaned, masked, and reshot the thing before I installed it:
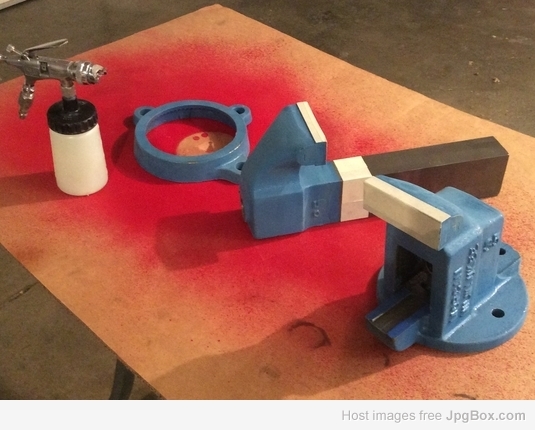
The castings had little prep, and what was there was a bit rough. There was cheap lube applied, a bit messy and not in a few areas I would have liked it to be. I cleaned it all off, and relubed with synthetic EP grease.
After the paint dried, I got ready to assemble and bolt it down:
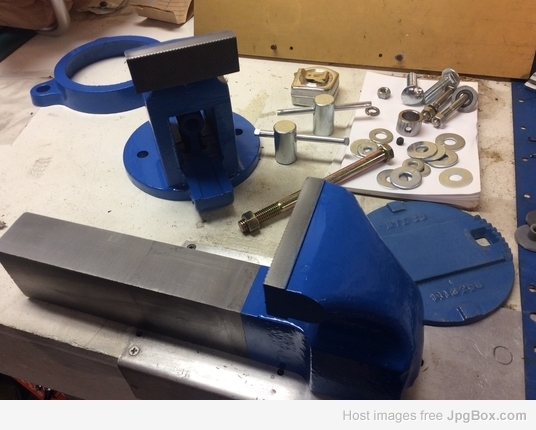

It sits on a 1/8 piece of formed aluminum that is bolted to the bench top. When I got it all done, I hi lighted the lettering, mostly because we are in the middle of an ice storm, and there was nothing else to do.
Another pet peeve. The screw and handle were raw steel, not so much as a smear of oil. Is it that tough or expensive to clear zinc plate the steel parts to keep them from rusting?
I cleaned the rust off it, and shot it with clear coat:
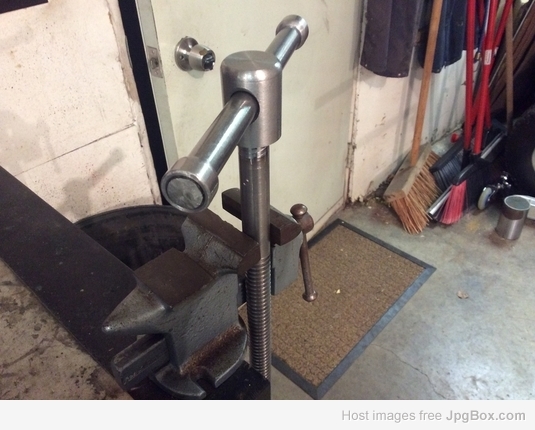
All done:
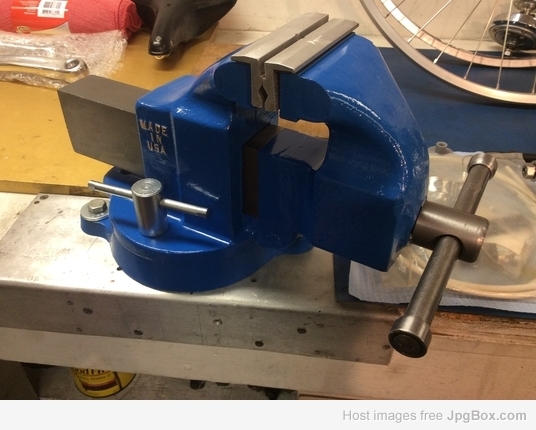
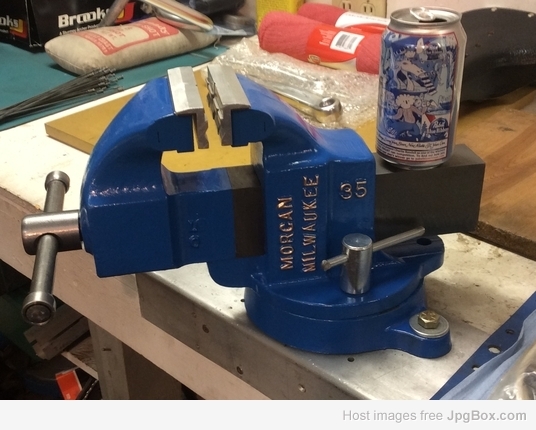
The aluminum soft jaws were from a different vise that happened to fit pretty well.I have sheet lead around the shop too, should I need something softer than the aluminum.
A used 3 or 4 Wilton would have worked well, if I could find a decent one-I never have. They are always priced really high, too, and usually need new jaws and a part or two, driving the cost up to higher than the equivalent size new Morgan.
Best,
Ted