Some of you folks may have read my posting A heavier gun required in which I renovated a rather old Baikal O/U shotgun that was fitted with a rather poor piece of Manchurian walnut for a stock, and the photographs in this posting are from that project.
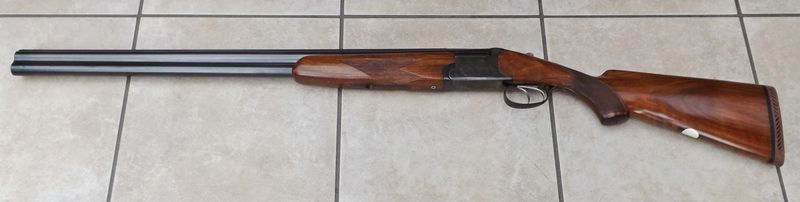
There are many gun stock finishes out there! This is my version of the tradition British classic oil based hand rubbed gun stock finishing method that was used on higher quality gun stocks during the late Victorian and early Edwardian era and in various forms today. But like a lot of things in life we have to make some compromises and gun stock finishes are no exception due to some of the more traditional ingredients being now rather difficult to obtain, and in many cases not worth the effort or expense to obtain them anyway. So to start things off I will do through the basic ingredients used and in doing so put some of the pieces in the history jigsaw of why choices of the ingredients where made and then abandoned.
Linseed Oil or the other name it can be found under in the edible types is Flax Seed Oil. Paint store Linseed oil has some inbuilt problems firstly there is a lot of foreign bits and pieces floating in it which goes under the cover all name Mucilage which all stems from the production process used to maximise the seed oil yield, and if you store a bottle for a year or so you will see how much of this foreign matter drops out as sediment in the bottle also this grade of oil also has a tendency to darken quickly when dry. Edible versions are far purer oils and the cleanest and purest of all so they tell me so are the Art grades of Linseed Oil, I have used this grade of oil and as yet I am still of the opinion it is not worth the extra cash. So for me Food grade is the oil I prefer to use because it is of high quality and being extremely clean it does not darken very much when dry plus it is of reasonable cost.
Walnut oil I have only ever found this oil in food or Art grades and needless to say I use the Food grade because the Art grades are far too high a cost so very poor value.
Now the drawback to using food grade oil is that you cannot purchase it with added metallic dryers or what is sometimes known a siccative. Paint store Linseed oil with an added dryer is known in the UK and may be the US as boiled linseed oil though still having purity problems so I do not recommend it. Though having no dryers is easily remedied by purchasing metallic dryers separately which are available US I believe and called Japan Dryers here in the UK known as Terebene Dryers and follow the instructions very carefully.
Tung nut oil I have nothing to say about this oil only buy the best you can afford with or without dryers the choice is yours.
Now after all of the above here in Brit land there is a supplier of many types of wood finishing supplies including oils whose products I am assured are above the usual paint store quality, retailing under the name of Liberon, I have not personally used any of their products so maybe a member who has can let us know what they think of them.
Now a little explanation about the oils we use firstly they are called drying oils because even without our help Linseed, Tung, and Walnut Oils all interact with the oxygen in the air (and to keep things simple) can I say dry even though it is a more complicated type of reaction and who cares any way! The Oils dry!!! So Tung and linseed dry coatings but not Walnut can stand up to a reasonable amount of ware keep the damp out of the wood to a point also enhancing the woods grain by soaking in at differing rates making the changes in grain structure stand out.
But oils on their own the finish is still bland so it wasnt long before a colouring agent was added to further enhance the woods grain (from now on my only knowledge is of what was used here in the UK) so artists colouring materials where used with some going far back into antiquity, though I feel that three deserve a mention because they still find their way in to those gun stock finishers potions that some folks collect as if it was a quest for the holy Grail.
MADDER ROOT which gives a red brown colour was one of the first gun stock stains to be used, first cousin to Alkanet and is still found in some finish mixtures though not so popular now.
DRAGONS BLOOD a tree resin a strong vermillion colour also like Madder root can still be found in some of todays finishes.
ASHPHELTUM (a posh name for Tar) brown to red colours can be obtained was also one of the first to be used, and worth experimenting with to match an exact colour in restoration work.
VANDYKE BROWN I only list this because it was very often mixed with the other colours in restoration or patch up work, can also be added to Alkanet (red oil) to tone down its red colour. A little explanation about this pigment is needed, here in the Brit Land artists Earth colours such as this one are actually Iron Ore and there are still small specialised mines producing many differing colours for the paint industry, also this type of colouring medium is extremely stable and not at all prone to colour change by exposure to sunlight.
ALKANET Ahhh! The Granddaddy of them all, has been used here in Brit Land since the time Stone Henge was a new build and Druids where colouring their skins blue with Woad, it was known in the past by such names as dyers Bugloss, Orchanet, and since Nicholas Culpepers Complete Herbal Alkanna Tinctora. It has many useful qualities but the main quality is it will give up its red colour in oil, mineral spirits and Alcohol so it became a dye colour every trade could use and of course it is cheap to produce you just grow it!
Finally because the surface finish using drying oils alone did not stand up to ware, acid sweat from hands over time tree resins and beetle lac where introduced to the mix this being the last ingredient of what we now call Gunstock Finishing Oil.
AMBER some finishers say the best producing the very finest finish of all, but is difficult to dissolve in oil unless treated and this treatment gives off toxic fumes so best left to the specialised varnish makers.
COPAL a tree resin another fine ingredient giving a fine finish but rather a purchasing minefield because of the multitude of types stick to finest art grades.
SHELLAC produced by a beetle rather than a tree, does not stand up to damp as well as Copal or Amber though Garnet shellac does have a use as a traditional finish.
COLOPHONY or ROSIN usually a pine resin this has been used in the gun trade since its early beginnings and still used today as flux for soldering and also as a constituent of some stock finishes in place of the more expensive Copal.
VENNICE TURPENTINE a form of resin made from boiling the highly resinous Larch tree sap, used by artists to give body to varnishes and oil colours sometime listed in old finishing oil formulas it does work but not that well and is mind stunningly expensive to purchase in artists grades.
CANADA BALSAM about the same as Venice turpentine but even more expensive you need to arrange a mortgage for its purchase here in the UK.
ALKYD RESIN this is the main corner stone used in modern paint and varnish manufacture and of course supersedes the other three resins I have little to say about it only that it is a good modern resin, and I am sure used in many modern stock finishing preparations that work exceedingly well.
THINERS not a lot to said about these they are either mineral or vegetable, such as true Turpentine or Turpentine substitute though the Artists versions are again far too expensive. Personally I do like to use true Turpentine but only for the smell because I just like it! The substitutes work just as well.
Thats the history bit over, now for how to make and apply my version of Brit vintage hand rubbed gun stock finishing oil that I used on my Baikal (a heavier gun required posting). But before you start this is a finish that is not applied today and the gun will be usable tomorrow, you must keep in mind that it is from an era where a mans labour time was not as valuable as it is today so patience is required but the finish is I think worth it.
You will need the following to make my version of a traditional gun stock finishing oil:-
One Ounce of Gum Copal Manila Purchase artist quality only other random offerings can and will cause you great problems because some Copals will NOT dissolve in Alcohol.
Two Fluid ounces of Alcohol (Ethanol) bio Ethanol is fine though do not use alternatives such as Isopropyl Alcohol it wont work!!!
One Fluid ounce of Linseed Oil food grade.
One Fluid ounce of Alkanet red oil your preference but I do use Andys version 50 50 edible Linseed and Walnut oils with Alkanet root pieces.
Red Oil is made by adding 60 grams (about 2 ounces) to half a pint (UK) of oil this makes a deep red oil whose colour can be lightened by adding more oil.
Half Fluid ounce of Turpentine or if you prefer a good quality Turpentine substitute I do use top quality versions of each. ** This quantity of half a fluid ounce is not set in stone but do not add more than one fluid ounce to the mix, it is there to prevent the oil becoming tacky too quickly as you rub.
As the quantities used are small use the best quality ingredients because I personally feel the cost is acceptable.
Now for the not so good news! I did say at the beginning that this finish comes from an era where time was not as valuable as it is today.
Firstly traditionally Red Oil is made from Alkanet root pieces soaking in oil for well over a year to enable it to reach that deep rich red colour, though I do believe if you use Alkanet root powder you can obtain the same effect after some months
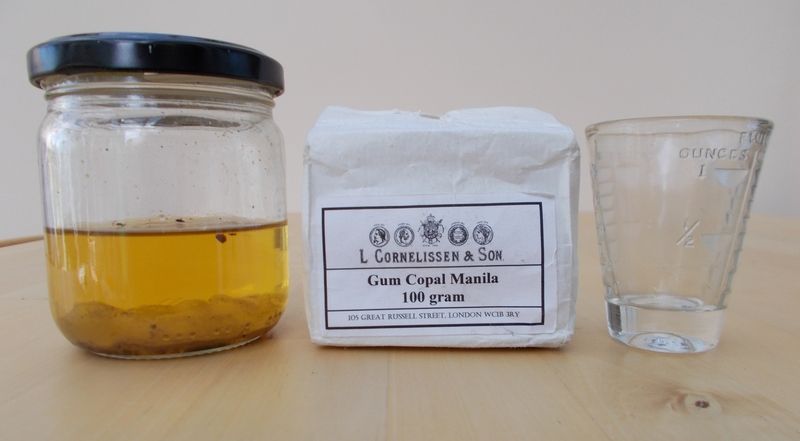
Next comes turning the raw Copal pieces usually complete with its foreign bits and pieces into a usable ingredient. So firstly break up the Copal into small pieces then place in a well sealing screw toped jar then pour in the Alcohol and screw down the lid tightly leave in a warm but not hot place then agitate the jar every couple of days. Eventually the Copal will start to dissolve but in its own time and in doing so all the foreign bits and pieces that was trapped in it will sink to the bottom of the jar forming a sediment leaving the liquid clear having a warm yellow golden colour as in the photograph.
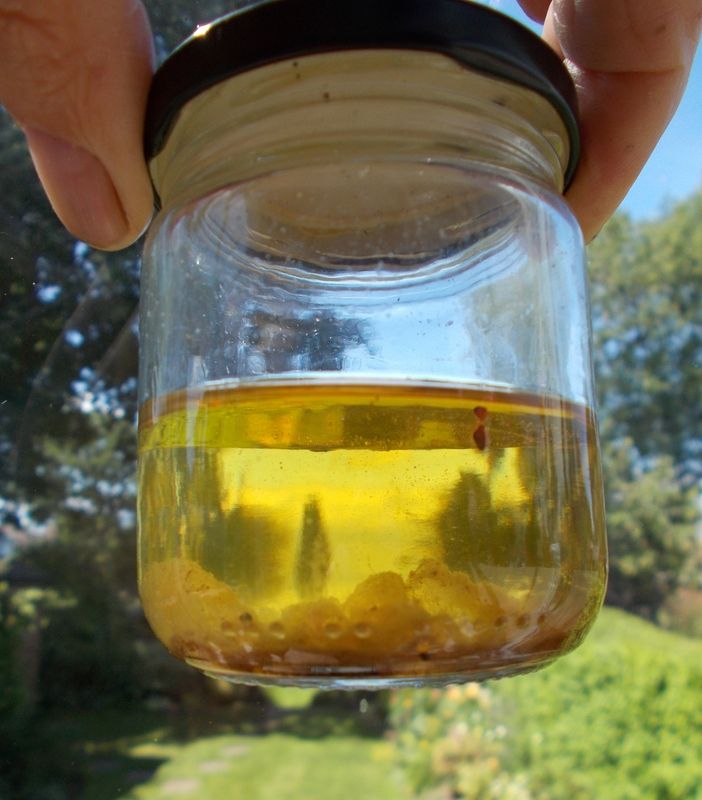
Then decant the liquid very carefully into a clean jar leaving the sediment un disturbed, a little help from pouring boiling water over the lid of the jar holding the Copal mixture will enable you to break the seal and remove its lid easily. At this point the alcohol is now no longer needed so we allow it to evaporate to the point that we are left with a thick syrup that we can use.
Now we add dryers to the Red Oil and the linseed oil but if you prefer to use a quality boiled Linseed oil only add dryers to the Red Oil, I use one level teaspoon 5ml of Terebene per ounce of oil. Then mix the Red Oil, Linseed Oil, Copal and Turpentine together this is my version of the traditional finish oil which you should store in a screw top bottle, now its shelf life is up to about two years and the reason for this is the oils and resin are contaminated with vegetable matter particles i.e. the Alkanet making things a little unpredictable you arent going to live for ever and Damascuss finishing oil is no different!
Now a short cut that you can use rather than preparing the Copal though I think any purists reading should think of what I say next as making a twenty first century finishing oil along the lines of what is in common use today. So substitute the Copal with 1 fluid ounce of a quality satin finish spar varnish though definitely not one with the dreaded polyurethane listed as an ingredient. There will be a high chance the resin used in the varnish will be Alkyd and yes it works extremely well, and when the finish is dry it also looks good too.
Because this information is rather large it will be posted it in two parts
The next posting I will describe how to go about applying this traditional finish.