Ted,
My post along with some of the other posts give the OP a little support in that he is not alone on having difficulty removing striker discs.
And, that, along with 50 cents, will get him a cup of coffee, exactly where?
Salopian,
Cole's tool has a continuation of sorts, past the relieved area behind the business end where the pins fit in-he drilled it far enough for the pins to drop into a second hole, in addition to the hole they are inserted into.
You can be sure the pins haven't skewed one way or the other in use by simply looking they are bottomed on the second hole. I suppose he could have simply made the holes full length, and not cut the relief just behind the business end, but, that wouldn't have been as elegant.
I usually put a small rare earth magnet on the shank, near the pins, to keep them in the tool. It does not look elegant, but, it keeps the pins from falling out of the tool. This is a view of the correct tool, for this application, in use. Having the correct tool can't be stressed enough:
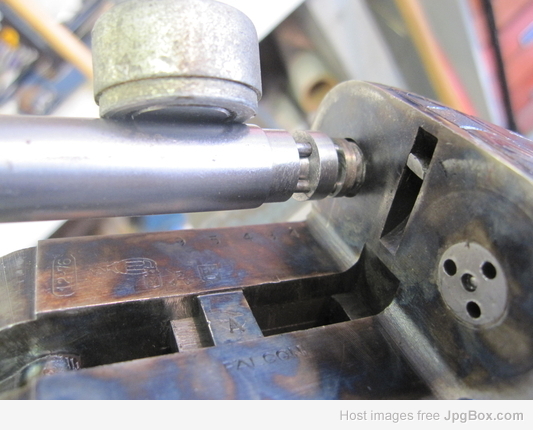
If I had a seized disc, I'd likely opt for the same treatment I use on other stuck fasteners, complete disassembly and a soak in a 50/50 mix of diesel fuel and automatic transmission fluid. In severe cases, I have rigged a double boiler to warm the concoction, but, the flash point is low, and it is a bit dangerous, something best done outdoors with plenty of ventilation. I've always let the seized fastener sit immersed for at least a week before the dreaded heating process begins, and, have usually been rewarded with parts that break free after the week. A few times I have warmed the mixture, and used a nitrogen spray on the seized part after removing it, to break the parts free. But, just the soak does wonders. I've left stuff sit for a month a few times.
I've dealt with many stuck fasteners in my shop, but, they are usually in an automotive capacity, not firearms. You are trying to save an unavailable part, and, time is your friend in this case. The first rule, old guns and old cars, is do no harm.
If you are unconcerned about the finish, you have the option of electrolysis, filling a plastic pickle barrel with wash soda, or, lye, water, and hanging an electrode in the solution (I use a chunk of stainless steel) along with your stuck part, and using a 12 volt battery charger to drive the rust off the part, and onto the electrode. You can google the process, it is brutal, but, the part will be rust free, unstuck, and clean when it is over, usually a day or three. Never, ever needed to use it on gun parts. I start with better guns than that.
If you guys are using the quill of a Bridgeport verticle mill to apply pressure, you are abusing the machine, and not getting anywhere near the force you could with the right machine. A Bridgeport is a good mill, but, the quill is light duty, and not suited for that use. Better, are the Gorton verticle mills, and the monster, the English built Balding Beaver. I have access to all three, and a very good machinist passed that tip along to me. This falls under the use the right tool heading.
Lastly, all you gents that got a stuck disc free, did you do this to make it easy for the next guy?
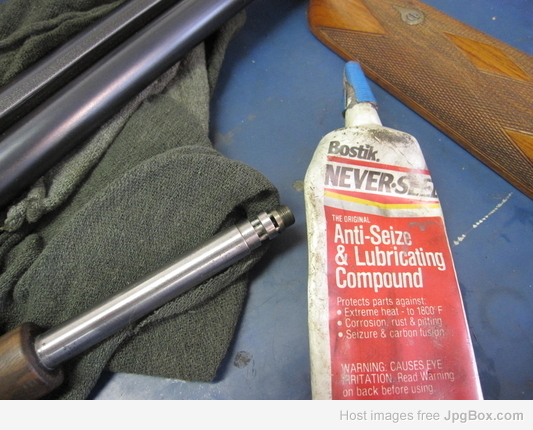
I am no more than a tinkerer on guns, perhaps an advanced tinkerer on Darne guns, but, I have some pride and always make the job easier for the next guy with the tools, on either a gun or a car. A tiny tadpole shaped spot of this ends any trouble with a stuck disc for more time than we will be alive.
Salopian, I hope I described the tool well enough for you to produce one, if you need a better picture PM me. I don't know the status of the other tool mentioned, but, I imagine ebay could be your friend if you need one.
Best,
Ted