S |
M |
T |
W |
T |
F |
S |
|
|
|
1
|
2
|
3
|
4
|
5
|
6
|
7
|
8
|
9
|
10
|
11
|
12
|
13
|
14
|
15
|
16
|
17
|
18
|
19
|
20
|
21
|
22
|
23
|
24
|
25
|
26
|
27
|
28
|
29
|
30
|
31
|
|
|
Forums10
Topics38,531
Posts545,924
Members14,420
|
Most Online1,344 Apr 29th, 2024
|
|
|
Joined: Jan 2006
Posts: 9,430 Likes: 315
Sidelock
|
OP
Sidelock
Joined: Jan 2006
Posts: 9,430 Likes: 315 |
Finally made it to Sherman Bell's recent DGJ article. He certainly articulates the difficulty in defining Pattern Welded Shotgun Barrels, but his use of terms probably only adds to the confusion. As he mentioned, the technology and terms certainly changed between W. Greener's 1835 book and W. W.'s in 1910. At this point we're all a bit like Justice Potter Stewart trying to define porn in 1964, "I know it when I see it." Unfortunately, Bell did not discuss the THIRD form of Pattern Welded Shotgun Barrel - Laminated Steel. As has been discussed previously, Laminated Steel differs from Damascus Steel in that: 1. Laminated Steel has a higher steel : iron ratio, with higher quality steel. 2. Laminated Steel starts with the iron and steel mixed together (puddled) in a semi-molten state (the bloom) which is then hammered or rolled into rods. Damascus starts with individual strips of iron and steel. 3. Laminated Steel rods are twisted less than Damascus (but may have a pattern and the barrels are then referred to as "Laminated Damascus") No one source is adequate to define the 3 forms of Pattern Welded Shotgun Barrels, but this is probably the best from a mid- 19th century perspective: Engines Of War: or, Historical and Experimental Observations on Ancient And Modern Warlike Machines And Implements, Including the Manufacture of Guns, Gunpowder, and Swords with remarks on Bronze, Iron, Steel, &c.Henry Wilkinson, M.R.A.S. London 1841 p. 70 Part III On The Manufacture of Fire-Arms, And Modern Improvements. http://books.google.com/books?id=0XJeF_o...w3u60I#PPA70,M1 Starting on p. 87 Forging of Gun-Barrels A description of Stub, Stub-Twist, Wire-Twist, Damascus-twist, Stub-Damascus, Charcoal iron, Threepenny skelp iron, Two penny or Wednesbury skelp, and Sham-damn skelp. The most approved modern method of converting…(horse-shoe nails)…into ( Stub-Twist) gun-barrels after carefully sorting and picking the, to see that no cast-iron or impurities are mixed with them, is first to put about half a hundred weight into a large cast-iron drum or cylinder, crossed internally with iron bars, through the centre of which a shaft passes, which is connected by a strap with a steam-engine, and the revolution of the drum actually polishes the nails by their friction against each other; they are then sifted, by which every particle of dust is removed. The steel intended to be mixed with them is clipped by means of large shears, worked by the engine into small pieces, corresponding in size to the stubs, and afterwards cleansed by a similar process. About 40 lbs. are thrown on to the inclined hearth of an air-furnace, where they are puddled or mixed together with a long iron rod, and withdrawn in a mass called a bloom, almost in a state of fusion, to be welded under hammer of three tons weight, by which it is formed into a long square block: this being put in, at another door of the same air-furnace, is raised to a bright red heat, and drawn out under a tilt hammer of a ton and half weight, into bars of proper size to pass the rollers, by means of which it is reduced to rods of the required size. p. 95 Possibly a description of what was later termed Laminated Steel For the finest description of (Stub-Twist) barrels, a certain proportion of scrap steel, such as broken coach-springs, is cut into pieces and mixed with the iron by the operation called puddling, by which the steel loses a considerable portion of its carbon, and becomes converted to mild steel, uniting readily with the iron, and greatly increasing the variegation and beauty of the twist. In whatever manner the iron may be prepared, the operation of drawing it out into ribands for twisting is the same. This is effected by passing the bars, while red hot, between rollers until extended several yards in length, about half an inch wide, and varying in thickness according to whichever part of the barrel it may be intended to form: these ribands are cut into convenient lengths, each being sufficient to form one-third of a barrel: one of these pieces is made red hot and twisted into a spiral form, by placing on end in the prong of an iron rod, which passes through a frame, and is turned by a handle, the riband being prevented from going round without twisting by means of an iron bar placed parallel to the revolving rod. The spiral thus formed is raised to a welding heat, and dropped on to a cylindrical rod, which being struck forcibly on the ground (called jumping) the edges of the spiral unite, and the welding is then completed by hammering on the anvil. The other spirals are added according to the length of the barrel, and the forging is finished by hammering regularly all over. The ends of the spirals should be turned up and united at each junction of spirals, to avoid the confusion in the twist occasioned by merely dropping one spiral on anther; but this is rarely done. Wire-Twist, of any degree of fineness, may be obtained by welding alternate laminae of iron and steel, or iron of two qualities, together; the compound bar thus formed is drawn into ribands, and twisted in the same manner as the preceding. p. 96 The iron called Damascus, from it’s resemblance to the celebrated Oriental barrels and sword blades, is now manufactured in great perfection in this country, as well as in France and Germany, and may be varied in fineness or pattern to almost any extent, according to the various manipulations it may undergo. One method is to unite, by welding 25 bars of iron and mild steel alternately, each about 2 feet long, 2 inches wide, and ¼ of an inch thick; and having drawn the whole mass into a long bar, or rod, 3/8 of an inch square, it is then cut into proper lengths of from five to six feet; one of these pieces being made red hot is held firmly in a vice, or in a square hole, to prevent it from turning, while the other end is twisted by a brace, or by machinery, taking care that the turns are regular, and holding those parts which turn closer than others with a pair of tongs, the rod is by this means shortened to half it’s original length, and made quite round. If only two pieces are employed to form the riband, one is turned to the right, and the other to the left; these being laid parallel to each other are united by welding and then flattened; but if three square rods are used, the centre one is turned in a contrary direction to the outside ones, and this produces the handsomest figure. By these operations the alterations of iron and steel change places at every half revolution of the square rod composed of twenty-five laminae; the external layers winding round the interior ones, thus forming when flattened into a riband, irregular concentric ovals or circles. The fineness of the Damascus depends on the number and thickness of alterations; but when wound into spiral form, and united on its edges by jumping, the edges bend round and the figure is completed. If there is one thing that I hope to accomplish with my personal investment in time, money, and an increasingly limited intellectual reserve  , it would be to create a common language of Pattern Welded Shotgun Barrels so we can communicate effectively. Our illustrations and Pete M's movie shows the HOW of damascus production. The method of twisting and the arrangement of the iron and steel strips in the 'lopin' or 'billet' primarily determine the pattern that is produced however. My approach is to define those patterns, so we are at least talking about the same thing.
Last edited by revdocdrew; 07/31/08 10:38 AM.
|
|
|
|
Joined: Dec 2001
Posts: 12,743
Sidelock
|
Sidelock
Joined: Dec 2001
Posts: 12,743 |
Drew; I do not have the DGJ, so cannot read Bell's take on this, but other than the inclusion of new patterns & also laminated steel, & the ommision of some patterns which had fallen by the wayside, I really see little difference between W & WW Greener's works of 1834 & 1910 pertaing to terminology of twist/damascus etc. From W Greener's 1834 work pertaining to the "Stub Twist" & "Stub Damascus" I do not get the impression the metal was brought to a melting (puddling) point but that the stubs & chopped coach springs were simply thoroughly mixed & brought to a "Welding Heat". At this point they would stick to an iron bar inserted into the pot & a large mass (bloom) would be withdrawn, put under the hammer thus completing the weld & forming into a bar. For Stub Damascus the mat'l was twisted in the bar, for Stub Twist it was not. I do not know if is just an "EGO" thing or what, but while Bell has had some valuable info I have been somewhat turned off by his seeming insistance on "Tearing Down" everything early writers have said on various subjects. A prime example was the long shell/short chamber subject, which was fairly well settled just prior to & immediately following WWII & throughly reported on by Burrard. Bell took everything Burrard said totally out of context, made a complete wreck of all the work which had been done by the British Manufactures Which Burrard reported on & strongly Implied that no positive conclusions had been drawn until "He Did It". In this case, as I see it, WW simply built upon the works W had started, I see nothing contradictory between them. Certainly time & experience had proved W Greener right in that steel was desirable (read that necessary) in the composition of a patterned bbl. W Greener had been emphatic about this in 1834 at a time when, according to him, some others made their bbls of all iron. In the ensuing years with the development of more powerful powder & heavier loads, many of those bbls discussed by W had simply proved inadequate & fallen aside. Also I believe that suitable "Stubs" had become mostly unavailable & so was virtually a thing of the past by WW's times. By the same token the fact that oil, drained from the head of the Sperm Whale, is unavailable to us today does not mean that firms such as Parker, Lefever, Smith, etal were wrong in recommending it ca 1900 as the best obtainable for oiling their guns.
Miller/TN I Didn't Say Everything I Said, Yogi Berra
|
|
|
|
Joined: Feb 2006
Posts: 3,737 Likes: 55
Sidelock
|
Sidelock
Joined: Feb 2006
Posts: 3,737 Likes: 55 |
Drew, I agree it would be nice to unitize the different kinds of Damascus along with the laminated and stub twist. An example would be what old L.C. Smith catalogs referred to the different grades having good, fine and finest Damascus. We know that this same type of nomenclature was used by Parker and other leading gun companies, and I'm sure their Damascus grades were the same but probably with a different name. So I have to agree that it would be nice to have a list of what they refer to and to have it universal.
David
|
|
|
|
Joined: Nov 2005
Posts: 4,598
Sidelock
|
Sidelock
Joined: Nov 2005
Posts: 4,598 |
To further confuse the issue... Whose definition of laminated? The English aka Greener? By the time WW wrote his book in 1910, he acknowledged that damascus was no longer being produced in England. There were multiple centers for damascus production, Belgium, France, Italy, Germany, Russia, Spain over this 100+ period. So what country and what time frame?
I see this as problematic for anyone who attempts to categorize, including Bell. While I have not seen / read his article, did he include any sources that were not English?
The production methods changed over this time span. As did the smelting.
Pete
|
|
|
|
Joined: Dec 2001
Posts: 2,399 Likes: 15
Sidelock
|
Sidelock
Joined: Dec 2001
Posts: 2,399 Likes: 15 |
I have seen two Ithaca Flues guns with one barrel twist, the other damascus. There is a picture of one of them in my book.
|
|
|
|
Joined: Jul 2009
Posts: 196
Sidelock
|
Sidelock
Joined: Jul 2009
Posts: 196 |
Drew/others Apologies for the basic query, but I noted this recent gun in the UK as having "skelp" barrels - the first time I had seen such a reference. http://www.byrnesauctioneers.co.uk/BidCa...tus=A&alot=Its apperance (albeit at a distance) appears quite mottled and not a regular pattern. Is skelp therefore a "lower" quality type of Damascus barrel? Forgive the ignorance - just interested to know. I am equally sure there are plenty of types of skelp - unfortunately have no further info.
|
|
|
|
Joined: Nov 2005
Posts: 4,598
Sidelock
|
Sidelock
Joined: Nov 2005
Posts: 4,598 |
Well, you are asking a good question. The methods kept changing over time and by country / region. Pictures are the best way to illustrate the process. As written descriptions become confusing. Early on, some makers would incorporate used horse shoe nails along with cut up wagon springs, etc. This is basically known as skelp. Then they would twist these rods together to add strength. Eventually they would wrap them around a mandrel to form a barrel. The "patterns" were difficult to control at best. But the British in particular had the skill to produce rather consistent patterns using this method. The "other approach" was to have the pattern formed by alternating layers of iron and steel. Eventually, these rods were produced solely by rolling mills. The rods were purchased by the barrel makers according to the orders they had for various quality barrels. An early tool. The perrot used to twist the rods. 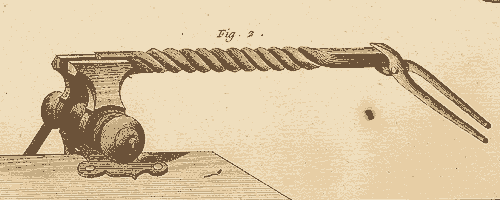 Belgian barrel makers with rods from the rolling mill. 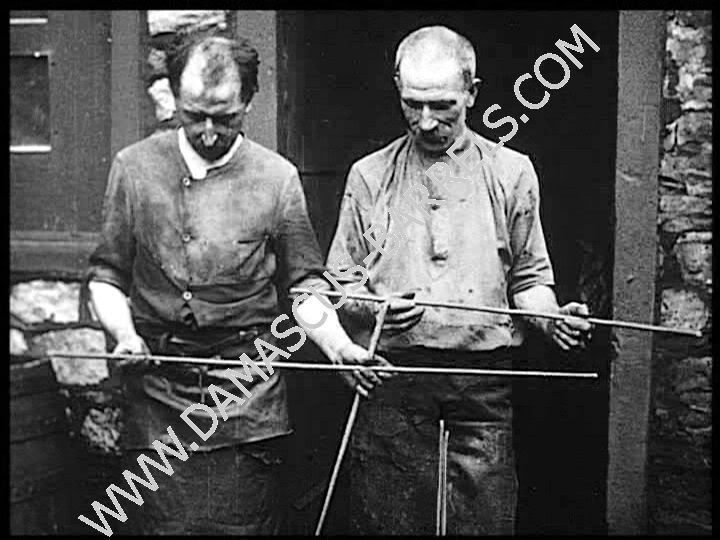 A Belgian patent showing the layout of a rod that will produce a star damascus barrel. 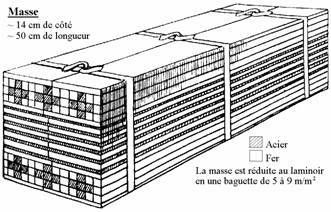 Belgian makers forge welding the rods around a mandrel. 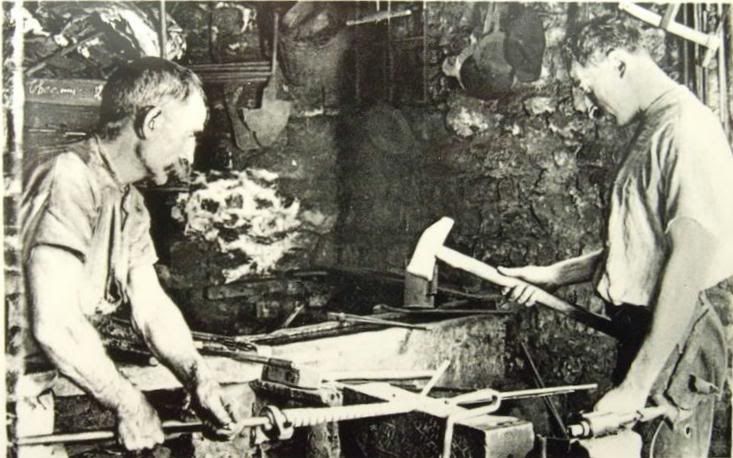 This is a barrel in process. You can see the chemise that protects the barrel from being welded to the mandrel. 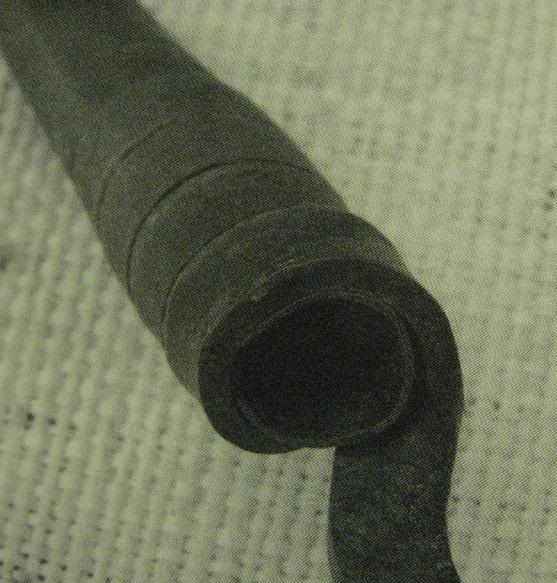 Very early recreation a skelp barrel being formed. 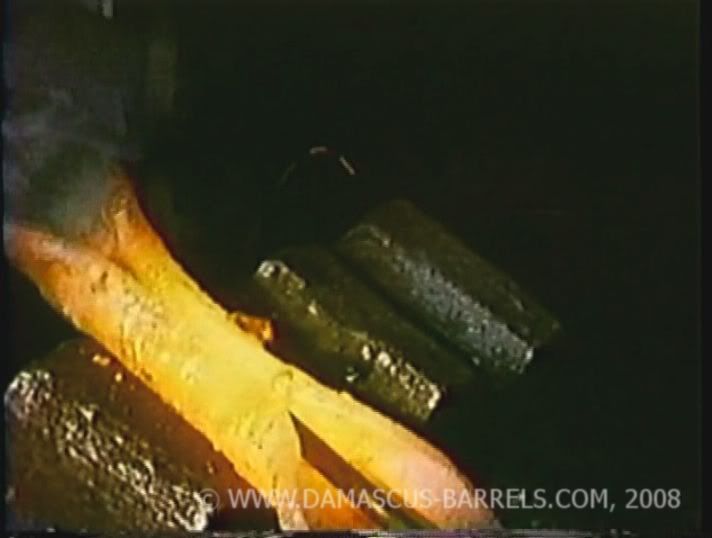 Here you can see the skelp material. They would attach the horse shoe nails by welding them and then beating them into shape. 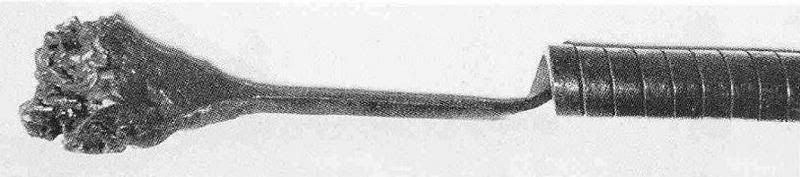 An English shop using a water driven trip hammer to form a barrel. 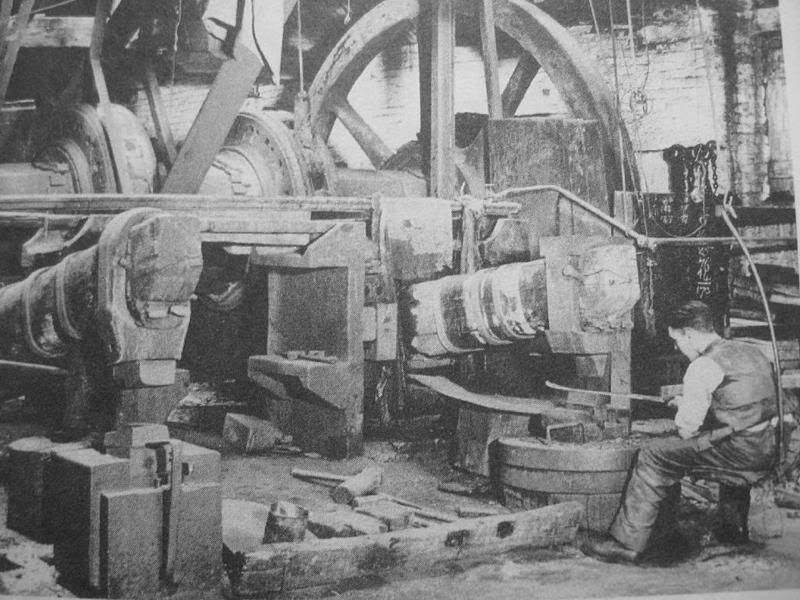 Some of the patterns from Greener's book. 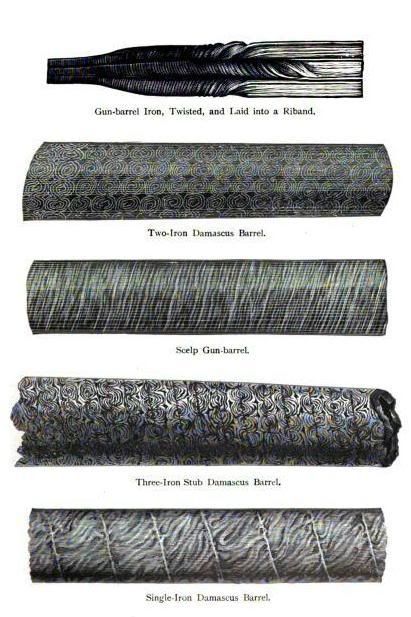 I should add that these are very late methods, from about 1780 to 1930. The origins go back hundreds of years to Asia and India. There were early patterns produced in India that the European makers could never reproduce. Pete
|
|
|
|
Joined: Jan 2006
Posts: 15,456 Likes: 86
Sidelock
|
Sidelock
Joined: Jan 2006
Posts: 15,456 Likes: 86 |
By the time WW wrote his book in 1910, By 1910 Damascus was literally a thing of the past.
|
|
|
|
Joined: Nov 2005
Posts: 4,598
Sidelock
|
Sidelock
Joined: Nov 2005
Posts: 4,598 |
In England damascus production had stopped. The Belgians continued into the 1930's.
In part, the huge WWI increase in steel production contributed to this. The steel industry needed to find other outlets for it's products and focused in part on sporting arms.
Smokeless powders really came into their own at this time, again a result of WWI.
Coupled with rising labor costs across Europe, this lead to the decline and eventual demise of damascus on a massed produced scale. The guilds had been on the wane for nearly 30 years.
In Belgium, some of the large arms makers turned their attention to the production of the automobile.
Pete
|
|
|
|
Joined: Jan 2006
Posts: 9,430 Likes: 315
Sidelock
|
OP
Sidelock
Joined: Jan 2006
Posts: 9,430 Likes: 315 |
Short version: English Twist was called "Plain Twist", "Birmingham", "Skelp/Scelp", and referred to as "Wire Twist" by W. Greener in 1835. This is Dr Gaddy's example Long version to follow 
Last edited by Drew Hause; 02/17/10 10:09 AM.
|
|
|
|
|