I'm getting close to finishing a PH 12ga, with a #2 frame. I'm going to French Polish this one, but I have a question as to what specific shellac to use.
I've already read the FAQ on original finishes over on the PGCA board, but the only reference to a type of shellac was to the orange variety, only one of many.
Does anyone have an idea what specific shellac was used? Was
it orange, amber or blonde? Was it waxed or unwaxed? Was it button or flake? Does anyone here have any idea?
I intend to initially build the base with a two pound cut, then topcoat with a one pound finish, pretty standard french polish.
Thanks
Kenneth
Ken, please share your experiences when the project is done. I've often considered using shellac but have been intimidated after reading instructions. Photos would be nice too.
I'll be sure to document the process.
eeb, thanks, I'm aware of the Bullseye/French Red filler approach, but I was hoping for a little more information as to the original Parker process...
I would recommend mixing your own from flakes. Garnet gives the deep red on dark woods. On blond wood I use button lac, it will give you the caramel color that lovers of French walnut crave. Just mix the quanity required. When fresh it is a much better product than it is in a month.
bill
Thanks. Garnet is available as dewaxed flakes. As far as button, do you suggest Kusmi #1 (caramel) or Kusmi #2 (red/brown)?
I'm leaning towards using the dewaxed garnet (2 lb. cut) as the base/sealer for the first 75 passes, then the caramel Kusmi #1 (1 lb. cut)for the last 25 finish coats. I'll then wax the stock as the final step, probably with Nufinish wax as it's got an advanced polymer in the forumla that provides UV protection.
Ken
Ken61, on the parkerguns.org website you should try a search on the forum. The late Austin Hogan posted an original recipe he used when touching up or completely refinishing an original Parker stock. Austin was highly respected among collecting circles and organizations. With a good bit of diligence I'm sure you can find it.
I did an LC with hand mixed wax free garnet shellac flakes w/a final coat of wipe on poly. I'd have to look at my notes, but I think I used a 1 or 2lb cut. Took me while to get process down on a practice stock, but it's a nice finish when you're done. Appropriate for a low grade gun IMHO.
This is my first picture I've ever posted..ever..hope it works! (gun is mine..couch isn't :))
Interesting. After reading through all the old PGCA threads,it appears Parker used Bullseye orange shellac. eeb, you were "on the money" as amber is the only colored shellac they now sell.
Nice looking LC. I've also got a Grade 0 (2 iron damascus) that I'll be starting on soon..
My practice gun was a Henri Pieper Eclipse hammergun..
Ken, prep your wood as you would for any finish. If I am working on an older gun I sand very lightly, just enough to knock down any grain that may have popped. This results in a nice antiqued finish that does not look so new. Take a couple cotton balls and bind them into a piece of old tshirt. With your finger dab a few drops of BLO (some recommend olive oil), and dip the tshirt into the shellac. Rub this with the BLO into the wood in firm back and forth strokes until it dries. Repeat doing small sections at a time. If you live in a low humidity area it goes quickly, otherwise you have to watch for tacky finishes and allow them to dry before proceeding. This method is detailed further on the PGCA website. It's not difficult and the results are pleasing, and while it's certainly not a London oil finish, it looks right on the older American doubles.
Thanks. That's what I'll do. I've also sent an email to Zinsser to see if they can provide me with the formulation for their circa 1900 orange shellac. Perhaps its the same as their amber product, possibly renamed for marketing purposes. Hopefully they'll respond with the info.
Ken
Phunter, here's an LC question. Were your barrels and receiver recolored? If so, how? I'm also set up for slow rust bluing as well as case coloring receivers, so any info on processes would be appreciated.
Thanks
Ken
French Polishing if done right is a very rewarding finish. As stated the wood has to be prepped. What you need is alcohol, shellac (Zinsser's Amber) 3-in-1 oil, a large cotton ball and a 4" square piece of lint free cotton material (old T shirt).
Soak the cotton ball in the alcohol and then squeeze it out. Wrap the 4" square piece of cotton cloth tightly around the cotton ball. use a popsicle stick or small piece of dowel and dip it into the shellac, and let a drop or two fall on your ball. Start at the hell, toe, and rub in a circular motion the size of a silver dollar and then lift off, do not let it sit on the wood at the end of your stroke. Put another drop or two on the ball and then put ONE drop of oil on it also, rub in a circular motion over the area you did and move but over-lap your previous spot. Do this over and over again until you are done. It takes about an hour to do the whole stock. If you decide to stop and rest, no problem, just begin again and go over the spot where you started.
The oil is added to help the shellac ball slide over the surface and the wood will not water stain.
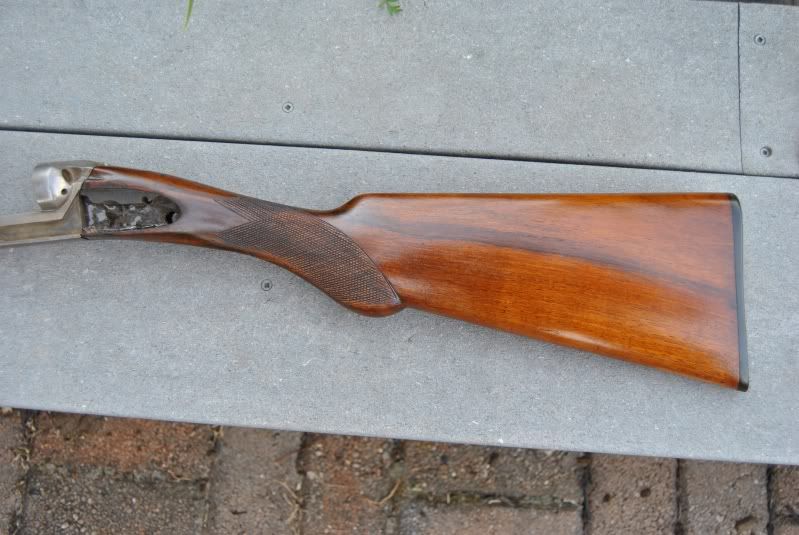
If you want to read the best book ever on French Polishing, get "Adventures in Wood Finishing" by George Frank.
Thanks. I'm fairly decent at the technique, due to other woodworking projects. I also lucked into a couple of old, unopened cans of Japan Drier (Redwing)at an estate sale, the stuff with all the old illegal antifungals in it (Mercury, etc.) so I can at some point try a traditional oil finish.
Here's a metal related question for anyone who has done this. In the PGCA FAQ on barrel refinishing, they recommend Watco Danish Oil (neutral) to coat the barrels. (Damascus and Twist) Would this also apply to receivers?
Ken
Ken, Watco or Formby's Tung oil work great on metal. Keep the coat thin.
Thanks. After more research I'm considering formulating my own Danish Oil. It's merely a combination of oil, varnish, sprit and drier, but making my own will allow me to add more Tung oil. At this time, I'm considering a 1:1:1 mix of Tung oil, polymerized varnish, and spirit. I'll then add a small amount of drier to the mix. Anyone else make your own?
I've never heard of using 3-in-1 oil to do a french polish. What benefits does the 3-in-1 have over linseed or olive oil?
"I've never heard of using 3-in-1 oil to do a french polish. What benefits does the 3-in-1 have over linseed or olive oil?"
And I have never heard of using linseed oil or olive oil.
Boiled Linseed oil in itself is a great finish. The ONE drop of 3-in-1 is all that is added every time you re-apply the shellac.
As to the reply from Ken, I have made my own trying to follow a recipe from 100 years ago. Can get pretty close with todays ingredients, but to tell you the truth, on a low graded gun you cannot beat True Oil.
Hmmm. I have been trying to get the 3-in-1 oil "out" of my gunstocks. I guess I'll have to rethink that.
Your method of using 3-in-1 is indeed interesting JDW. I won't argue with your results.
Sure, I'm not knocking True Oil, I just consider that the concept of "Restoration" to be that of matching original appearance/techniques/materials as closely as possible.
Ken, not to be smart but if you want to replicate the original finish that was on the lower graded guns, easy, brush on shellac and that is it.
Daryl, I am guessing all the oil that is found in stocks is linseed oil, especially if it is hard. There was a period back then when people had read articles on preserving the wood and bringing it back to what it was when it left the factory. The trouble is, they never read the whole process and never took the receiver from the stock.
Factory for an oil finish was to submerge the stock in linseed oil and let it sit for a day and rub it out. Again and again and then to use some of the recipes they had for a final finish. This process might take close to a month.
I still can't comprehend using that much oil on the barrels and receiver to seep into the wood with the gun standing.
Here is an FW S L.C. Smith post 1946 Field Grade stock that I finished for a gentleman that wanted the whole gun taken apart and the barrels, receiver, screws, trigger guard and was sent to Classic Guns for re-rusting, re-case hardened, along with Nitre bluing of the trigger guard.
In my opinion Classic Guns does the best in reproducing the colors of an L.C. Smith.
I refinished this stock using 16 coats of True Oil. Sorry about the dark photo, but I decided to take the pictures at the last moment.
Beautifully done, David. Would you be willing to share your step by step process applying the True Oil?
Thanks Joe, but it was really simple. The receiver was off and the only thing I did was lightly sand the wood. I didn't remove all of the old shellac, just dulled it and applied the True Oil with a small piece of cotton linen a drop or two at a time. Once you get a few coats on the farther the True Oil seems to go. I try to apply this in a circular motion also, but in some places it is hard to do. You will see if you miss a spot as it will be dull, just go over it later and it will blend in.
In your dry area, you should be able to apply 2 or more coats a day, but if it starts to stick, stop and wait for it to completely dry.
Hi all
Now I do not want to be controversial over what are good or bad gun stock finishes but the old adage of if you could ask a hundred gun stockers here in Brit land what was in the finish they use you would get a hundred different answers, but I am sure that in a lot of the answers they would be extremely economical with the truth anyway.
Now over the years I have collected a lot of so called hush hush and highly secret recipes for gun stock finishes including the infamous secretive ‘Slakum’ to the trade mix it by the gallon and use a big brush to apply it.
And in a nut shell they all have roughly the same type of make up but using a large variety of ingredients to do the same thing.
So to make sense of it all I started to list the ingredients by what their part in the formula was and it started to make sense to why there are so many versions of finishes.
Though if you look back in to the past fine wood finishing was the territory of Musical Instrument makers and what substances they had to choose from was extremely limited by today’s standards.
To keep things practical it is a lot easier to have a liquid to apply rather than a solid lump so we need a carrier that will either hold in suspension or dissolve what we want to apply to the wood. And what we would want to apply is either a simple basic wax or drying oil to various forms of resin though if we go down the resin route drying time starts to become an issue with some resins though not in every case, but some unknown and unsung hero found that if lead salts where added into the mix it would shorten the drying time or dry a mixture that normally would not dry of its own accord.
So what are the traditional ingredients of these usable mixtures?
Carriers
Oils Drying. Tung. Linseed. Walnut. Poppy.
Non drying. Almond. Olive.
Volatile carriers. Alcohol. Tutpentine. Oil distillates.
*Now the drying oils can be a carrier and the finish*
Resins Copal. Venice Turpentine. Canada Balsam. Pine resin.
Amber. Shellac.
Wax Bees. Carnuba.
Sicative Heavy metal salts.
Now there are some items I have left out and of course we now have synthetic versions.
So one of the many versions of Slakum I have
Boiled Linseed oil (It is not really boiled it is oil with a Sicative added)
Turpentine
Carnuba wax
Venice turpentine
Alcohol
Some versions add Antimony chloride to darken the wood also plaster of Paris to act as grain filler.
One of the trade finishes make it by the gallon sort of thing consisted of.
Alcohol
Pine resin
Finely ground glass cullet as grain filler.
The final polish was given to the stock with wax.
One of the most expensive
Walnut oil with Vandyke Brown Artist oil paint added
Amber This is prepared by roasting and it gives off extremely noxious vapours
Talcum powder as grain filler
Turpentine.
Terebene dryers
So to me they are all versions of the same story with a twist here and there.
And finally one recipe given to me by a professional member of the gun trade though it was some time ago now but if the truth be known it my be still in use.
50/50 turpentine and polyurethane varnish adding it smells ok and when you give it a final polish it looks ok to and a lot cheaper.
As for my self I use red oil on the stock for the colour then a couple of coats of Talcum powder mixed in Garnet French polish to seal the wood and fill the pores applied with a brush then cut back to the surface. Next a mixture of artist’s refined linseed oil and turpentine with Terebene driers as finishing oil. With that classic dull sheen given to the stock using a wax polish I did make my own but I now use a polish by Fiddes & Sons the best I have come across. I use this oil wax finish on gun stocks because it is waterproof extremely flexible scratches do not show very much and you can always re finish it by just applying a little oil with your hands and re waxing.
For those interested in French Polishing, there are a few good videos on U Tube and also a great write up on Wikipedia.
Here is what I use along with the cotton ball/s and cotton fabric for the pad. Some use cheesecloth, I have but doesn't hold up long and then you get strings of cloth in your finish.
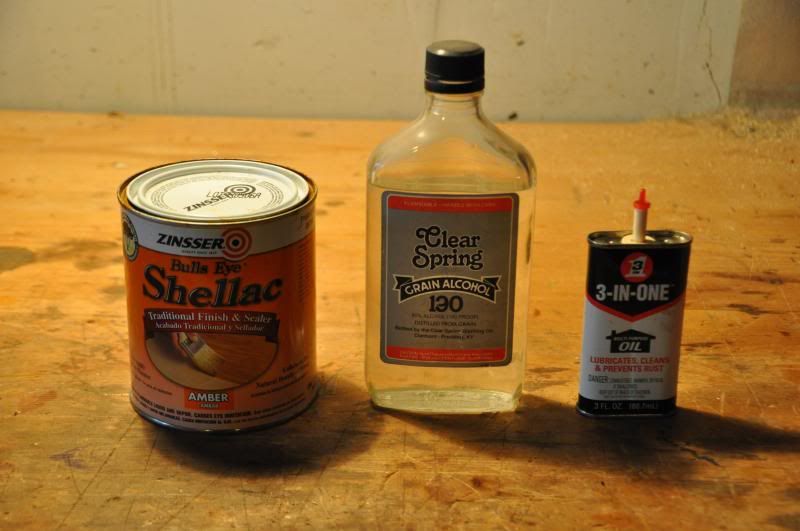
This picture is about as large a project that I can handle comfortably. it is about 21" in diameter and is a replica of a Shaker snake foot candle stand.
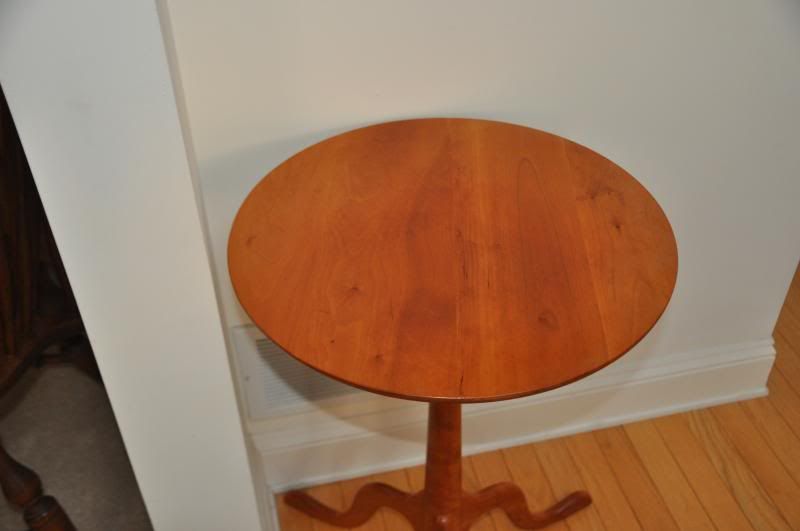
Damascus was posting his as I was writing mine. As he said there were many types of stains, and ingredients for that "perfect" finish. Thanks for posting it, and please post a picture of your finish.
Excellent work David. You're right, I'll probably end up with a simple shellac coating on the wood.
damascus, thanks for the info, I'd always wondered about "Slakum". In your recipe, does "Venice Turpentine" mean the thick, artist-grade type? Also, are the amounts of the three main ingredients equal?
By the way, what are your opinions on an initial weak solution Copper Sulfate soak when refinishing damascus or twist barrels? Is it superior to a 10-15% ferric chloride etch?
Thanks
Ken
Thanks Ken.
Damascus, years ago I loved to refinish old bamboo fly rods, strip the old silk thread and alligatored varnish off. You talk about trade secrets, in the hey day of bamboo fly rods the finish put on was to each maker and kept a secret.
I had found that using spar varnish was very close and the trick was to use very thin coats and to use a fine tip camel hair brush to get no air bubbles. The results looked great especially using silk thread and if a light yellow was used, the finish was almost translucent. That was when I didn't need glasses to see the windings.
Thanks. Good timing, I've got three I need to refinish at some point. Too bad none of them were made by Orvis, I think one is a South Bend and another is a Heddon. For my fine work I use a bench mounted extendable magnifier with a built-in fluorescent light. Other than that, I'm only up to 1.75X on my reading glasses...
Hi JDW
I have come up with some photographs of the traditional oil and wax stock finish that I have used on a vintage London double which is now close to one hundred and fifty years old so a high gloss finish I feel would be well out of place on such an old gun. On the first photograph I removed the wax and in doing so removed the shine but it allows you to see the grain of the timber, in the other photographs I re waxed the finish again to give the stock some lustre.



You did mention using ‘Spar Varnish’ and at the time Victorian/Edwardian gun makers where experimenting different ways of finishing gun stocks a Mixture of Spar Varnish and Turpentine was a popular finish of the day, the reason being that the original ships spar varnish formula consisted of Copal dissolved in Tung nut oil and a fine finish it made.
Ken61 I have only used the ‘Venice Turpentine’ that is intended for the treatment of horses hoofs well I am sure if you used the artists variety you would have to arrange a mortgage to purchase an ounce or two I find the horsy stuff works fine.
And as it is your original post I will not feel that I am hijacking it to change it to barrel finishing. I do not use Copper Sulphate bath at all because of the risk of copper plating, but I do like to start the browning process with a Ferric Chloride bath which I feel keeps the action of the rusting solution in the early stages constant and making the rust deposit less patchy.
There are a number of ‘Slakum Formulas’ but the most common one is :-
˝ Pint Boiled Linseed Oil
2 Ounces Plaster Of Paris
˝ Ounce Antimony Chloride (If you want to darken the wood)
˝ Gill Alcohol
2 Teaspoons Venice Turpentine
Rather a lot for single person use but it can be adjusted down in quantity.
I do feel that I should say here it is not a magic substance that will work perfectly with no effort or practice because it wont!!!!!!!!!!!!
damascus,
Turpentine for horse's hoofs? Ah yes, I recall reading about this about forty years ago in James Herriot's "All Creatures Great and Small". I'm not sure if this is currently used like that over here. Kind of like Terebene, which appears to be unavailable. Since I live out here in the sticks (Eastern Iowa) and horses are much more numerous than artists, next time I trot over to my local farm supply store I'll see if they have some.
Thanks for the etchant info, I'm still deciding which may to go, the copper sulphate method I'm considering is the one described by Tony Treadwell.
Thanks
Ken
Thanks Damascus for your photos. I agree, a high shine on a old gun does not look right. On some of these guns that are done to a high finish, a little pumice and oil with take care of that. I have even used polishing compound that is used on cars.
Ken is Japan Dryer or Dryers available on your side of the pond in all but name it is the same as Terebene. I am sure that any oil paint drying accelerator will work and the only reason I mentioned it is I prefer to use art quality Linseed oil rather than the oil found in paint stores. The Linseed Oil be it boiled or raw sold in paint suppliers is rather impure and seems to deaden the grain somewhat and darken quickly over a short time. The art grade is far cleaner and does not seem to darken with age but it is far slower to dry and that is the reason for adding the dryers.
Yes, it's available over here. As well as the artist grade linseed oil. I'm going to mix up some slakum and test it out..
Thanks
The Bullseye people have responded. According to them, their current amber product is essentially the same thing as their orange product circa 1900. It is a natural, uncolored product with minor coloring variations from batch to batch.
Damascus, here's two more questions. Would Slacum be a more appropriate finish for a lower grade Birmingham gun from the mid-late 1800's? Over here I often run into these older hammerguns with Birmingham proofs. The second one is about your "Andy's Formula" for alkanet oil, in two parts. First, would there be any detriments or benefits of reducing the amount of linseed oil, even to the point of using straight walnut oil? I'm wondering if linseed was used because it may have been considerably cheaper. Secondly, Would an initial alkanet spirit stain (alkanet steeped in grain alc.) be beneficial to start the coloring process, followed by application of the oil?
How is your percussion restoration project coming?
Ken
Hi ken
Slakum was reputed to be used by a number of Victorian/Edwardian London gun makers but there has never been an official pen to paper it is only rumour. A lot of the so called secret trade finishes where passed about verbally and some where written down by some ones grandfather. The thing about all the finishing formulas you can never really be sure if there is something added to the formula just for the hell of it or to hide the correct constituents of the formula. Now the problem with Birmingham guns is that in the hay day of Birmingham gun making the trades men could make any quality of gun you requested from the absolute pinnacle of the art to rather poor trade quality. So because a gun has Birmingham proof marks will not always be a clue to its quality for example my Purdey has a full set of London and Birmingham proof marks and I have seen a number of Birmingham produced guns of superb quality having no name.
Now as for Andy the wood’s red oil formula he reckoned that by using a 50/50 cut of Walnut and linseed oils the colour of the oil was more stable and would keep in the bottle much better and not tend darken as linseed oil usually does, I do not think increasing the more expensive Walnut oil would make any difference to the end result only the price. Using alcohol rather than oil is another way of extracting the colour from Alkanet and some finishers prefer to use this method, because it speeds up the whole process though the final colour of the stain is far richer if the Alkanet is steeped in oil. In a nut shell the cheaper the gun the less will be spent in its entire production and that would include its finishing so more than likely it would just be the cheapest of timber and stain to darken it the cheapest stain at the time to use was asphalt and finishing with a couple of coats of linseed oil and a little wax polish to improve the look. Now on let’s say one of the top makers of Birmingham or London the stock was an all important eye catching part of the gun so more time effort money and finer timber was sure to be invested in its final finish, hence the use of resins to produce a lasting more pleasing finish to the wood of the stock.
As to my percussion project it is as we say over here ‘on the back burner’ because just before Christmas I purchased a black vintage ‘Oak and Leather case for my Purdey’ in extremely poor condition, I did post how I restored the leather and now I have just finished all the internal case repairs plus re-styling the partitions. So I am on the final part of the restoration re-lining with baize, I have taken some photographs of the process and I will post it when the case is finished in the near future.
Damascus,
I note that Antimony Chloride is listed as an optional component of your "Slakum Formula" to darken wood & if I remember correctly I have seen this in other "Slakum" Formulas in the form of "butter of antimony".
Can you elaborate on the impact Antimony has on darkening light wood. How much does it darken it & what is the color imparted?
The reason I ask is that I've found some of the lighter colored wood difficult to stain dark enough & get the "correct" color & especially when viewing the finished wood at different angles & in strong light.
Just wondering what the possibilities are & I'm assuming that Antimony had a definite purpose or it wouldn't have been used.
Hi Brittany Man.
Unfortunately I can not give you any information regarding the effects of Butter of Antimony (Antimony Chloride) because I have never added it to a finishing oil, my preferred method of finishing a stock is to apply the colour directly the wood be it either Alkanet Vandyke Brown artists colour, or sometimes Potassium Permanganate. Then fill the grain and finally apply the finish because I have found that if I apply a coloured or a finish that will colour the wood in some way it always well in my case it does, turn the stock colour patchy in the extreme.
I can only suggest that a little experiment is needed using Antimony but as I have said if you obtain the correct stock colour before you apply the finish there is really no need to apply a finish that will darken it further.
damascus,
A few more questions. Do you have any idea what the amounts of copal and turpentine were used in the early spar varnish mixtures? I suspect that this may be a more period correct mix for older lower grade Birmingham guns. In "Andy's" recipe, was it boiled or unboiled linseed oil? Could you add Vandyke Brown to this recipe as part of the staining process?
Thanks
Ken
Hi ken
As far as I know spar varnish was bought in from specialised varnish manufactures it would not be cost effective to manufacture in small amounts. It is possible to purchase traditional spar varnish today but it will be at a price, though you could possibly find more information regarding spar varnish on the internet. I know this may be heresy to some folks but in its day spar varnish was the finest available so by thinning it made it perfect for applying by rag brush or hand on gun stocks amongst other things, and in our time polyurethane varnish far out performed other varnishes on the market and has been used in exactly the same way as spar varnish and I will put my hand up to doing it!!!!!!!!
The ‘red oil’ has always been manufactured from Alkanet root only, by adding Vandyke brown to the mix you will remove that unique red colour. Quality ‘Vandyke Brown’ pigment used in artist colour is manufactured from Iron Oxide and because of this it is extremely permanent and stable, because of this it is used to colour grain fillers as well as being used as a wood stain in its own right. The linseed oil in Andy’s version of red oil is raw oil that is no drying agent is added though the only difference between boiled and raw linseed oil is the boiled dries much faster.
Damascus,
Here's what I found. Any suggestions for modifications for use on stocks? Linseed, Tung or Walnut oil?
Copal Varnish For Fine: Paintings, etc
Fuse eight pounds of the very cleanest pale African gum copal, and, when completely run fluid, pour in two gallons of hot oil; let it boil until it will string very strong; and in about fifteen minutes, or while it is yet very hot, pour in three gallons of turpentine, got from the top of a cistern. Perhaps during the mixing a considerable quantity of the turpentine will escape, but the varnish will be so much the brighter, transparent, and fluid; and will work freer, dry quickly, and be very solid and durable when dry. After the varnish has been strained, it" it is found too thick, before it is quite cold, heal as much turpentine and mix with it as will bring it to a proper consistence.
Read more:
http://chestofbooks.com/home-improvement...I#ixzz2tJPPaLAZThanks
Ken
Damascus,
I appreciate your response re. the use of Antimony Chloride.
I remember a comment about it's attempted use & and abandonment in one of Don Masters books.
Reading between the lines I'm thinking it was a "quick & dirty"
way of darkening light colored wood w/o the time & effort required by the traditional "red oil" method which does take some time for drying.
However, I would still like to give it a try on a piece of scrap just to see what the results are.
Hi Ken sorry for the delay in replying I went on a fast trip to London to collect some parts for another back burner restoration project though not gun related.
I would stick to the well tried and tested formula for copal varnish and use Tung nut oil, I have made a form of copal varnish in very small amounts though quite a considerable time ago but according to my notes you use 2 parts Copal resin and I suggest artist quality to 3 parts oil. The oil will need to be extremely hot for the copal to dissolve as for adding the turpentine to the hot mixture I would give that a definite miss. Very hot oil and flammable turpentine could only be a recipe for a fire ball disaster, when the oil copal mix has cooled down it can become very thick then you add the turpentine to adjust its consistency to what you require.
Thank you damascus,
And to all you others who have contributed to this thread....
Ken